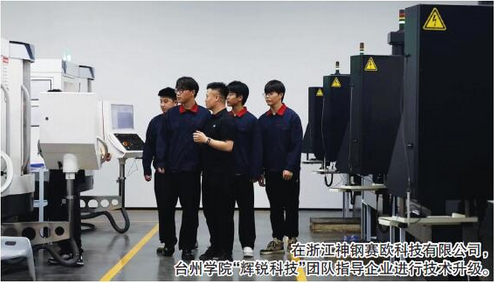
模具制造是我区的传统支柱产业。近年来,我区深入实施创新驱动发展战略,全力培育新质生产力,积极与国内科研院校人才团队合作,着力解决模具产业上下游“卡脖子”的核心共性问题,加快科技成果转化和产业化,推进模具制造做深做精。
“它的前角、后角等角度要按照我们给你们的制作手册来进行加工……”这几天,在浙江神钢赛欧科技有限公司,来自台州学院“辉锐科技”团队的技术人员,忙碌地在车间里指导员工提升硬质合金刀具性能的加工指标。
刀具是“模具的牙齿”,它的质量是制约高端模具制作精度和加工效率的重要因素,但一直以来,国内的高端硬质合金刀具由于技术不足,存在烧结温度高、断裂韧性不足等难题,长期依赖于进口。
面对模具刀具的“卡脖子”难题,我区携手台州学院共建模具技术研究平台,依托浙江省工量刃具检测与深加工技术研究实验室,经过艰难技术攻关,打破了混合粉体制备瓶颈,攻克了制备温度过高等一系列制造难题,实现刀具的“坚不可摧”。“通过我们的核心技术使金属钴的含量大幅度减少,并且能够大幅度提升它的硬度、耐磨性和使用寿命。”台州学院“辉锐科技”团队负责人彭科瑞说。
目前,该人才团队与我区多家模具龙头企业合作,成功研发出新型的硬质合金技术,实现高端硬质合金刀具国产替代。“像原来我们用日本刀具加工,比如钢料的沟槽只能够加工到12厘米,现在跟高校的团队合作以后,能够达到40厘米,刀具的耐冲击性都有明显提高。”浙江神钢赛欧科技有限公司开发应用部经理罗江涛说。
加快解决“卡脖子”难题,我区还积极开展补链强链专项行动。近年来,我区模具产业引进80多家高科技企业,着力做好模具科技前端研发,包括模具设计系列、模具编程系列和模具检测系列。按照省、市深化传统制造业改造提升,建设了模具博览城和模塑工业设计基地、模具智能小镇。在模具工艺方面,实现了全国领先的数控机床模具工艺流水线的全替代,并以永宁江科创带建设为牵引,营造有利于模具产业高质量发展的政策环境、法治环境、竞争环境、要素环境,不断提升黄岩模具数字化、智能化、规模化、集群化水平,打造具有国际领先和国内引领地位的世界级智能模具产业集群。
近日,在浙江精诚模具机械有限公司车间,服务于锂电池产业链的锂电隔膜模头正在加班加点赶工。“我们的订单基本上都排到10月份,晚上也经常都要加班赶订单。”浙江精诚模具机械有限公司涂布事业部总监蒋业龙说。
“爆单”源于精诚踏准新能源的产业风口,更关键的是企业组建人才攻关团队,20年如一日地攻关锂电隔膜模头的“卡脖子”难题,不断研发提升模头的精度和宽度,并新建恒温洁净精密检测车间和精密抛光车间,以国际同步的精密加工及检测设备,在材料选择、生产工艺和性能参数等方面,实现了与欧美和日本行业标准相媲美的水平,解决了锂电隔膜模头的国产替代难题。
“难度最主要的还是精度,要达到头发丝的1%,现在精度和订单短交期方面我们比国外做得更好。”蒋业龙说。
同样,在浙江台州美多模具有限公司,该企业的拳头产品“大型精密复杂空调件注塑模具”正源源不断地供给美的、格力等知名企业的配套供应商。该产品刚刚入选2023年度“浙江制造精品”名单,有效解决了国内大型复杂精密模具注塑精度等方面的技术难题,实现了国产自主替代。
“我们30年专注于空调件、冰箱件等注塑模具的制造加工,在技术上具有‘补短板’的作用,提高了大型家电类模具的注塑效率,降低了模具的制造成本,打破了国外对于高精度模具市场的技术垄断行为。”浙江台州美多模具有限公司机加中心部长郑才利说。